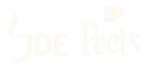
The Quality Analyst is responsible to perform quality checks on received goods and produced goods to enable the delivery of products that meet the required specifications.
Provides input to warehouse team which received goods are to be released for production and which are to be returned to supplier.
Provides input to warehouse team which produced goods are to be released for customer shipment and which are to be blocked for rework / scrap.
Provides guidelines to production team on how to rework product that does not meet the required specifications.
Safety
Quality:
Leadership:
engagement and ongoing improvements
Delivery & Cost:
Education
Experience
💼 What's Brewing for You:
- Competitive salary
- Exciting allowances to perk up your day
- Meal subsidies (because great coffee needs great snacks!)
- Sports perks to keep you energized
- What's next? Enjoy unlimited free-flow coffee and tea on us! ☕🍵
It’s amazing what can happen over a cup of coffee. At JACOBS DOUWE EGBERTS (JDE), we’ve made it our mission to find out. Our people have been raising the bar since day one, thinking fast and acting even faster to make an impact that’s felt around the world. JDE is the home to some of the most well-known coffee brands in the world.
For more than 265 years, we have been inspired by the belief. Today our coffee & tea portfolio is available in over 140 countries around the world through iconic household names including: Jacobs, Tassimo, Moccona, Senseo, L’OR, Douwe Egberts, Super, Kenco, Pilao & Gevalia etc.
It’s amazing what can happen over a cup of coffee. At JACOBS DOUWE EGBERTS (JDE), we’ve made it our mission to find out. Our people have been raising the bar since day one, thinking fast and acting even faster to make an impact that’s felt around the world. JDE is the home to some of the most well-known coffee brands in the world.